Underground corrosion is a function of several factors, which makes it difficult to give a generalized statement about expected service life. However, by considering the factors that affect corrosion rate coupled with engineering experience over the past 60+ years, an engineer or contractor can make reasonable predictions about the service life of a helical anchor.
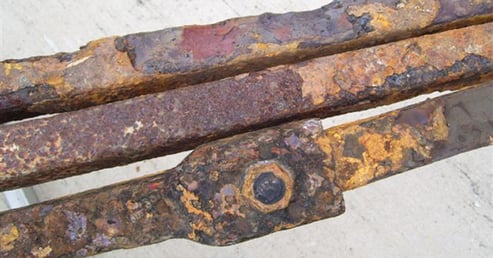
Some variables that effect underground corrosion are:
- Soil Type
- Moisture Content
- pH (Neutral soils with pH~7 have lower corrosion potential)
- Resistivity
- Location
Soil sampling and field testing can help determine soil type and properties that will affect both the anchor’s holding capacity and its expected service life. Knowing about the site conditions will aid in determining which guy anchor, helical pile, or resistance pier will provide the capacity necessary for a sure, functional, proper installation over time.
Soil pH and resistivity can be measured directly in the field as part of the geotechnical investigation. Resistivity, the measure of how strongly the soil resists or conducts electrical current, is often measured for substations and tower structures in order to design the grounding system.
Per the Federal Highway Administration (FHWA), the following criteria describe a mildly aggressive soil. The corrosion rates normally associated with Table A-3 are listed below the Table.
Electromechanical Properties of Mildly Corrosive Soils, Table A-3
PROPERTY
|
TEST DESIGNATION
|
CRITERIA
|
Resistivity
|
AASHTO T-288-91
|
> 3000 ohm-cm
|
pH
|
AASHTO T-289-91
|
>5 < 10
|
Sulfates
|
AASHTO T-290-91
|
200 ppm
|
Chlorides
|
AASHTO T-291-91
|
100 ppm
|
Organic Content
|
AASHTO T-267-86
|
1% maximum
|
The design corrosion rates, per FHWA-SA-96-072, suitable for use in mildly corrosive soils having the electrochemical properties listed in Table A-3 are:
For zinc:
- 15 µm/year (0.385oz/ft2/yr) for the first two years
- 4 µm/year (0.103 oz/ft2/yr) thereafter
For carbon steel:
- 12 µm/year (0.308 oz/ft2/yr)
You will find in most cases with CHANCE helical anchors and piles, manufactured by Hubbell Power Systems, Inc., these corrosion rates will result in service life exceeding 50 years. Service life is typically defined as loss of the zinc coating plus about 10% of the steel substrate.
Corrosion Protection Options
If, upon evaluation of the corrosion-causing factors listed above, you determine the need for corrosion protection for anchor products, several options are available to coat the metal and extend its service life. For example, the graph below from the American Galvanizers Association relates zinc coating thickness to service life. The thicker the galvanized coating, the longer the service life.
Hubbell galvanizes steel anchor and foundation products per both ASTM A153 and A123. The average coating thickness for CHANCE products is 4 mils. The graph shows 4 mil thickness results in an average service life over 50 years.
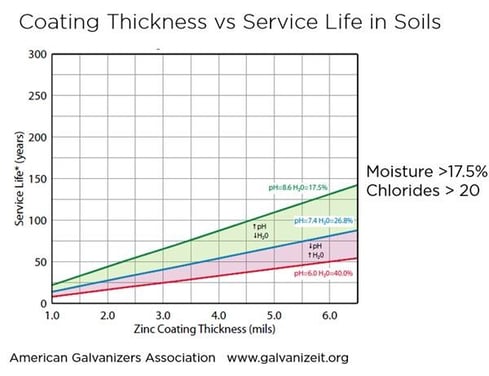
There are four types of corrosion protection typically used for steel foundations and anchors. They are listed in increasing order of cost:
- Sacrificial loss of steel, i.e. "corrosion allowance" (may vary based on region or engineer preference)
- Hot-dip galvanizing
- Other coatings - above grade and top 2 meters of soil
- Coal Tar Epoxy
- Paint
- Grout
- Sacrificial anodes (magnesium or zinc bags)
Read about an installation in a brackish Georgia swamp where coal tar epoxy was used to provide extra protection against the briny coastal soil, improving the longevity of the helical anchors.
Other factors that can affect service life of steel anchors and foundations are induced current, stray current, eddy currents, etc. It’s best to isolate the anchor materials from any induced, stray, or eddy currents. All these factors need to be evaluated specifically at each anchor location to best assess the overall corrosion potential.
For a more in-depth discussion of the factors that cause corrosion of helical anchors, review Appendix A of the CHANCE Technical Design Manual.