In the rare instance you encounter issues installing CHANCE® PISA® anchors (power installed screw anchors), take time to analyze what challenges arose.
5 QUESTIONS TO HELP IDENTIFY THE PROBLEM
1. Is there an anchor shaft fracture?
Look at the tooling anchor damage caused during the installation. A common problem for PISA anchors is an anchor shaft fracture during installation. Driving the anchor requires significant force and that torque is transmitted from the anchor installing wrench to the anchor helix via the anchor shaft. Therefore, if the anchor shaft stress exceeds the shaft’s ultimate strength, the anchor shaft will fracture.
What to do?
If you experience a fracture, recover at least part of the anchor shaft and observe the fracture surface. This is usually quite easily done; just withdraw the anchor rod, and you should find the top part of the anchor shaft still attached. Use this as a guide when installing future anchors.
2. Is there insufficient wrench engagement?
If the fracture surface intersects the drilled hole in the shaft (see Figure 1 below), insufficient wrench engagement was the problem. The PISA® anchor system is designed so the wrench, when properly engaged, bridges the hollow section of the anchor shaft, preventing it from carrying any significant torsional load. If the wrench does not engage
the anchor shaft sufficiently to bridge its hollow section, the section becomes the weak link in the system and fracture occurs well below the anchor’s rated torsional strength.
What to do?
To avoid a recurrence, use the same type and size anchor, but be sure to screw rods all the way into the anchor and couplings. Lock the anchor assembly into the wrench with the locking dogs, and follow the anchor during installation maintaining proper down pressure at all times. Fracture problems occur with the square shaft (SS) anchor if the anchor shaft is not pinned into the wrench, couplings are not properly bolted up or they are subjected to gross misalignment.
3. Is the anchor shaft not pinned to the wrench, are couplings not properly bolted up, is there gross misalignment?
In either of the first two cases, the shaft tends to work its way out of the wrench or coupling. Once it gets far enough out that the drilled section is loaded torsionally, it breaks well below its rated strength (see Figure 2 below).
In the third case, the bending moments at the joints cause gradual “belling out” of the coupling (see Figure 2 below) again leading to torsional loading of the drilled section and rating. In all cases, the fracture surface intersects the drilled hole. In the latter two cases, failure usually occurs below the ground line and only visual inspection of the coupling shows the difference.
What to do?
To avoid recurrence, make sure that the coupling bolt goes through coupling and shaft, rather than passing above the shaft end. Pin the top shaft into the wrench during installation, and avoid misalignment along the anchor shaft or between anchor and Kelly bar. 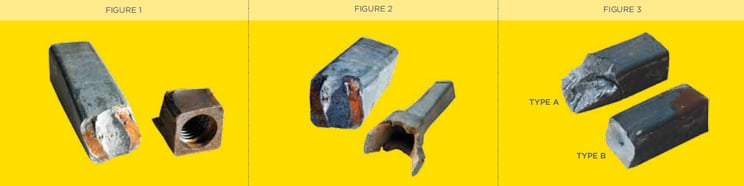
4. Are there stress conditions?
The result is that the stress conditions causing fracture are triaxial, not torsional and Type A fractures are neither unusual nor indicative of brittle material. There are claims that a helical-end wrench, which engages the anchor shaft along the upper helix surface, increases the torsional capacity of the anchor by forcing it into a Type A fracture which naturally has a larger fracture surface area than a Type B fracture. Actually, such wrenches offer little practical advantage because most of the time they merely force anchors to fracture the way they would anyway.
What to do?
If you rule out wrench engagement problems, there are still a couple of possibilities left. If the anchor seems to be encountering obstructions, or the operator does not seem to maintain alignment, impact loading or excessive bending moments may cause the anchor to fracture at reduced torque.
5. Is there a hard stratum at an oblique angle or obstructions in the ground?
The anchor’s striking obstructions in the ground may also affect the stress conditions.
If a hard stratum at an oblique angle to the anchor’s path is the problem, change the anchor batter so that the angle is closer to 90 degrees if possible, or stop down pressuring the anchor as it reaches the stratum and allow it to auger a “pocket”, which will counteract the tendency to lead off. In obstruction-laden soil, be prepared to remove the anchor, move over, and try again if the anchor starts leading off.
Other Helpful Tips
- If you rule out wrench engagement problems, try the same type and size anchor again but with slower rotation speed and additional operator care.
- If the soil seems homogeneous and the alignment is maintained properly, try a smaller or higher-strength anchor.
Remember that installation torque is an indication of soil strength, so if the torque is higher than expected, the soil must be stronger than expected and a smaller anchor should develop the load.
