In the event of a fault current, milliohms can make the difference between a lineman going home for the day or being seriously injured or killed. With fault currents in the tens of thousands of amps or more, the parallel path to the lineman needs a resistance so low that milliohms do make a difference.
Small Change has a Big Impact
Small changes in resistance of the ground set in parallel with the lineman can have a big impact on the voltage through the lineman’s body. For example, to maintain a maximum of 50 volts across a lineman whose body resistance is 1,000 ohms during a 20,000-amp fault current, the parallel protective ground set needs a resistance of approximately 2.5 milliohms or less. A loose or corroded connection could significantly increase the ground set’s resistance and the voltage through the lineman. For example, an increase of just 20 milliohms would allow the voltage across the lineman to reach approximately 450 volts. This is well above the acceptable level and jeopardizes the lineman’s life.
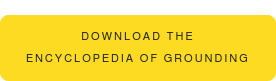
Considerations to minimize resistance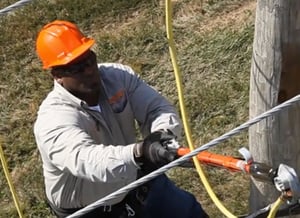
- Cable size – Larger copper grounding cables offer lower resistance and thus an opportunity to reduce the overall resistance of the ground set. Consideration for the weight also comes into play as the larger cables are heavier. The utility must decide what size is best for their maximum available fault current and application. If the adequacy of the cable size is in question, it is better to go with the larger size.
- Cable length – The longer the cable the higher the resistance. To minimize the resistance of the ground set in parallel with the lineman, we need to minimize its length. It should have some slack so it is not taut, but excess slack adds unnecessary resistance that would result in higher voltage through the lineman in case of a fault current.
- Inspecting, cleaning and testing – Ground sets should be inspected and the contact surface areas cleaned before each use. The inspection should include checking for loose connections, contamination and corrosion, and any damage to the clamps, ferrules, or cable. As some damage and contamination or corrosion in the connections cannot always be detected in the regular inspection, periodic testing should be performed to ensure the ground set’s resistance is within satisfactory levels per industry standards and to keep the voltage through the worker to an acceptable level. Please see the April 10, 2018 blog post on Care & Maintenance of Personal Protective Grounding Equipment for more details.
Small details can make a big difference when it comes to the safety of the lineman. Paying attention to those details can shave off the milliohms that make the difference. It is of utmost importance that crews are properly trained. Contact us for a free grounding consultation or customizable in-person training.