Hot line maintenance appears to have begun in the early 1900’s with a few homemade tools. Tools and working methods improved vastly in the following decades. During that era, linemen realized the value of a protective shield to guard them and the equipment they were using from accidentally contacting an energized conductor.
Much of this early “cover-up” was made of natural rubber or some type of phenolic material. Even wood was used during the 1940s when World War II efforts created a shortage of rubber. Materials and manufacturing methods have advanced a great deal since those early days, but one basic principle persists: You must respect and care for your equipment.
Field care keeps new quality.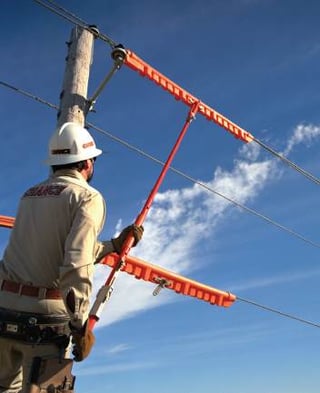
At Hubbell Power Systems, all CHANCE® temporary cover-up equipment for accidental brush contact has been design tested per industry standards to ensure that each new cover leaving our factory will meet the applicable testing and performance standards.
But what protection does this same cover afford after it has been used ten times, after five years . . . or in 10 years? Will it still be sound and clean enough to provide the intended protection? To help answer these questions and add to the life of your equipment, here are some basic cover-up care procedures:
- Thorough visual inspection before each use,
- Careful handling during installation and removal,
- Thorough cleaning,
- Periodic electrical testing,
- Proper storage
Take a close look – regularly. Visual inspection of each cover just prior to use is extremely important. Do not assume that a cover is sound and ready to use without closely examining it. Rubber covers such as line hose and blankets can be deceptive, in that the material can close back after being cut or mechanically punctured. The established method of inspecting rubber equipment is to stretch the surface which exposes the damage. This can usually be accomplished with a rolling or peeling action. Both the interior and exterior surfaces must be inspected.
Remember that you are also looking for excessive contamination, moisture, swelling, and surface crazing.
Damage to hard plastic covers is usually more obvious than with the rubber equipment. Each cover should be inspected inside and out for cracks, deep gouges, and contamination. Check to make sure all brackets and/or handles are secure and that all fasteners are in place.
If there is any question at all that a cover may not be suitable for use, it should be immediately tagged or marked and set aside for later cleaning and electrical testing, or disposal.
Train for handling skills. It is important that line workers become acquainted with any unfamiliar cover-up equipment on the ground before actually using it up on the pole. A line worker needs to know how it is to be adjusted, installed, coupled and removed. Rough handling can do a great deal of damage and shorten the life of the cover-up equipment. At the end of a work session, never drop the covers from the pole top to the ground. Instead, lower them carefully with a hand line. Remember that both plastic and rubber cover-up becomes stiffer and more difficult to flex as the temperature drops. It can be helpful to warm a cover in the truck cab before using it on a cold winter day.
Clean for electrical integrity. Proper and frequent cleaning may be the most neglected procedure of all. Dirt, creosote, wire markings, and other contamination can be conductive, especially if combined with moisture. Many covers are slid along a conductor surface, pole surface, or cross arm surface during installation and removal. This sliding action picks up many kinds of contamination and can result in scratches and gouges. It is also important not to use tape on covers such as rubber blankets. The tape can leave behind sticky residue that can collect contamination resulting in electrical tracking. The point at which a cover should be cleaned before further use is whenever it appears “dirty.” Some covers could be considered dirty after only one use, while others could be used many times before cleaning. Some utilities inspect and clean cover-up on a regularly-scheduled basis. This can save headaches and loss of equipment use later.
Strong household and industrial cleaners can cause permanent damage to some cover-up materials. For example, some industrial solvents will dissolve ABS plastic and swell some rubber compounds.
Mild soap and water are recommended for cleaning all of the cover-up materials. Sometimes, for the more stubborn spots, an additional sprinkle of “elbow grease” and a nonabrasive pad will help. Be sure to rinse thoroughly to remove all soap residue and wipe away all moisture from the cover’s surfaces before using. If anything stronger than mild soap and water is to be used, it is essential to first know what material is being cleaned and what effect the cleaner will have. The product description in the CHANCE catalog (Section 2400) usually specifies the material used in each cover. Use this information with caution since designs and materials can be changed without notice. If still unsure of the material being cleaned, wipe a cloth saturated with the intended cleaner along one edge of the cover. If any orange color is transmitted to the cloth or the cover surface dulls, do not use that cleaning solution.
In general, polyethylene material can be cleaned with most cleaners, but ABS plastic and rubber material are much more restricted and can be easily damaged. Moisture Eater II cleaning solvent is excellent for cleaning stubborn dirt, tar, and metal rubbings from CHANCE flexible line hose and rigid polyethylene covers.
Testing used cover-up. Some electric utilities have established periodic retesting programs for cover-up equipment. New cover-up from CHANCE meets or exceeds industry standards and can be put into immediate service after initial inspection for shipping damage. Anytime that the electrical integrity of a cover is in question, it should be tested at a prescribed withstand voltage according to its rating or discarded. Rubber insulating blankets are required to be electrically retested at a minimum once every 12 months after being placed into service per ASTM F479. ASTM standards F478 and F479 describe testing methods for rubber equipment while ASTM F712 deals with testing of rigid plastic covers. If it is determined that a cover does not meet electrical requirements, it should be permanently marked or cut up so that it cannot be placed back in service. CHANCE cover-up is intended for temporary use only. If installed for more than 72 hours, the covers should be removed from the line, cut up and destroyed or visually inspected and electrically re-tested before being placed back into service.
Store properly. Improper storage can cause a cover to become distorted, making it hard to use and possibly unsafe. Cover-up equipment should always be stored in such a way that the original intended shape is preserved. Many covers are designed to have specific air gaps and flashover distances in order to achieve a designated electrical rating.
Any distortion can alter the electrical characteristics. All cover-up should be stored in a clean, dry and protected location away from sun light, heat, and ozone. It should also be positioned so that the shape is maintained. Prolonged exposure to the elements can cause plastic and rubber to degrade, losing some of its flexibility, impact resistance, and electrical withstand properties. Do not store protective covers on top of a line truck. Rubber blankets can be stored flat or loosely rolled and placed in a blanket canister (see CHANCE catalog numbers C403-2998 and C403-2999). Flexible line hose should be laid horizontal and straight. If piled, be sure that the bottom units are not distorted by the weight of those above. Plastic covers can sometimes be nested together as long as there are no distorting forces applied.
Remember, personal protective cover up equipment will only protect you, if you take care of it!
