Common Corrosion Prevention Methods
Corrosion attacks steel parts every day, beginning the moment they’re produced. Variables including material, coating, and geographic location can either speed up or slow this activity. Reducing the effect of corrosion helps strengthen your utility lines and saves maintenance costs over the service life of the system. Several methods are common.
Hot-Dip Galvanizing
The most common method in fighting against corrosion in the utility industry today is hot-dip galvanizing (HDG). This process applies a sacrificial zinc coating to the surface of steel parts to extend their functional life. HDG has been the most cost-efficient and effective means for protecting steel against corrosion. It can often provide a service life exceeding 30 years.
However, in certain areas like coastal or industrial zones, HDG is not sufficient and service life can be reduced to 5 years or less. In these instances, utilities must turn to additional processes or alternative materials to protect critical components on their lines.
Secondary Processes
Frequent Inspections and Replacement
When secondary processes are employed in highly corrosive areas, the first approach is often more frequent routine inspection of critical items. In this case, components are evaluated to determine whether they’re beyond their functional limits and replaced as necessary.
Cathodic Protection
As a preventative measure, additional cathodic protection may be employed as well. Using principles like the HDG coating itself, cathodic protection programs require a sacrificial element (usually zinc) to be connected to the steel structure or component to further prevent corrosion. This also requires monitoring and occasional replacement.
These methods have two things in common:
- When done correctly, they can extend service life and protect against critical failures
- They require recurring investments of time and money beyond the initial HDG installation
Stainless Steel
When secondary processes are not enough, utilities turn to alternative materials such as stainless steel which increases the initial investment considerably.
The Thermal Diffusion Galvanizing Distinction
Thermal Diffusion Galvanizing (TDG) is a process in which zinc powder vaporizes under controlled conditions and diffuses into the surface of steel parts. Hubbell Utility Solutions has partnered with Distek NA to offer TDG hardware with improved corrosion protection using their ArmorGalv process and materials.
Distek developed the process in 1993, improving upon the basic ideas of Sherardizing which have been in use since 1904. Today, ArmorGalv is approved and used by major utilities, automotive companies, and all branches of the US military.
Applying TDG is very different than HDG which centers around dipping parts through a series of tanks—first cleaning solutions like hydrochloric acid, then molten zinc baths.
In contrast, TDG parts are cleaned with a simple wash and blasting system. Then they’re processed in a computer-controlled oven with a proprietary zinc powder mix. Under properly controlled heat, the zinc sublimates and diffuses into the surface of the part.
The result is a more uniform zinc-iron alloy that offers greater resistance to both corrosion and abrasion. This is further enhanced with the ArmorGalv coating by finishing the process with a proprietary sequence of topcoats.
Compare the Performance
The performance of TDG coatings in a standard ASTM B117 salt spray test far exceeds that of HDG. The evidence is shown in the photos below.
500 Hrs Salt Spray (Machine Bolt)
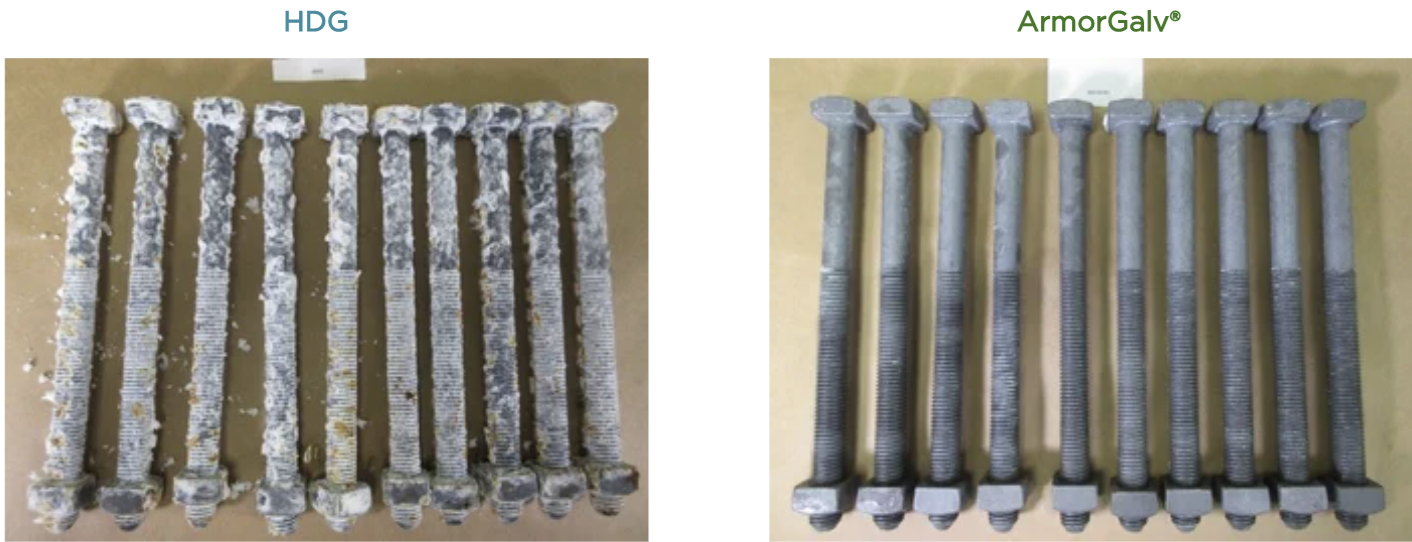
5,000 Hrs Salt Spray (Machine Bolt)
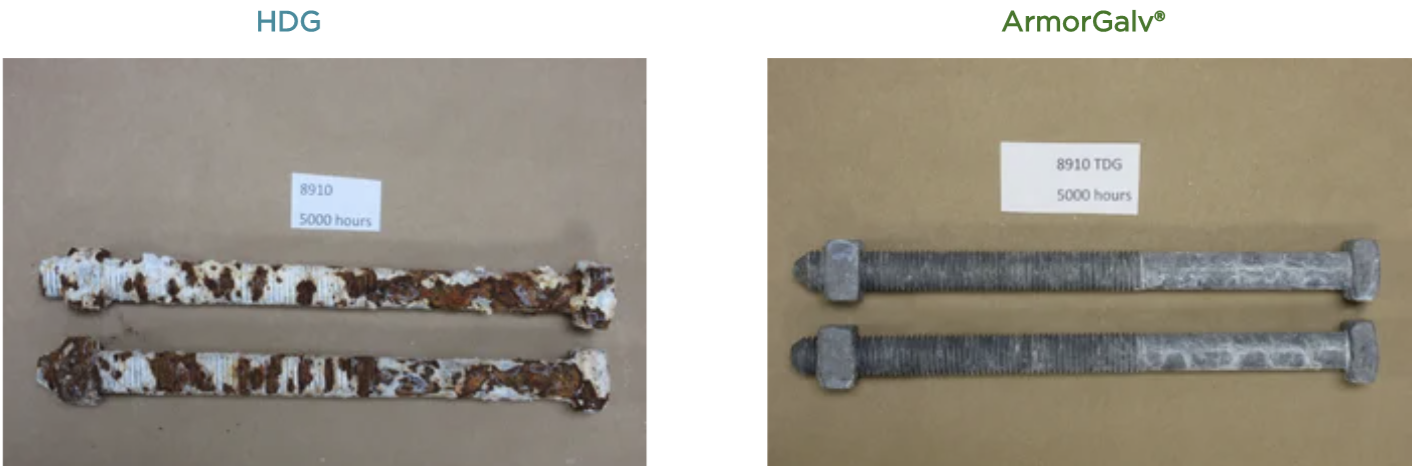
Figure 1: HDG vs. ArmorGalv machine bolts after 500 and 5000 hours of salt spray tests conducted in accordance with ASTM B117.
In these tests, HDG machine bolts began showing signs of rust at just 500 hours and were nearly unrecognizable at 5000 hours. The ArmorGalv hardware remained largely unchanged. Comparing functionality was similar. The square nuts of HDG bolts began to seize up after 500 hours while the ArmorGalv assemblies operated as if they were just taken out of the box.
When is TDG Right For You?
HDG remains cost-effective for corrosion protection in most applications. However, this is not the case in highly corrosive environments like coastlines. HDG requires additional resources in these conditions, like those described above—recurring inspection, replacement, cathodic protection programs, etc.
TDG involves a slightly higher initial investment compared to HDG but remains significantly lower than that of stainless steel. Consider the below scenario in Table 1 for an area that experiences significant corrosion issues.
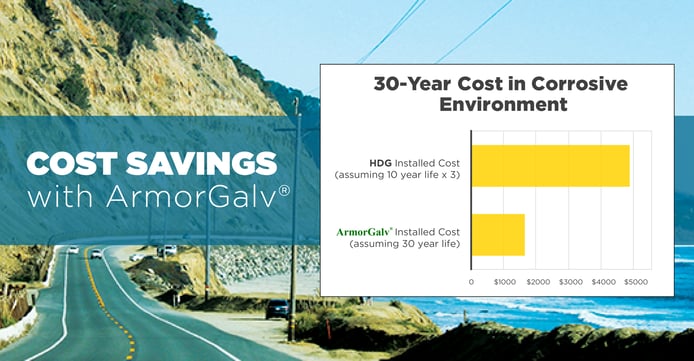
Table 1: Crossarm installation and maintenance fee schedule for HDG and ArmorGalv parts
In this example, look at the cost of a 30-year service life goal in an area that only experiences a 10-year service life for HDG. The initial investment upgrading to TDG is significantly less than the cumulative replacement costs of using HDG when equipment mobilization and labor cost are counted multiple times.
Assumptions and construction design will vary by location. Even so, it is apparent that TDG offers significant long-term savings when considering costs incurred over the life of the system.
Conclusion
Hubbell recommends TDG coating to maximize corrosion protection in harsh environments, product quality, and cost effectiveness. Learn more about Hubbell’s simple solution to savings on pole line hardware using ArmorGalv corrosion protection at hpsdelivers.com/ArmorGalv
