A common question asked by engineers and contractors is “how does anchor spacing affect uplift and/or compression capacity of helical anchors and piles?” Most building codes require a reduction in axial capacity for pile spacings closer than 3 pile diameters on center. This is known as group effects. Codes further state group effects shall be evaluated using a generally accepted method of analysis. The “standard rule” for center-to-center anchor/pile spacing used by Hubbell Power Systems engineers is an S/B ratio of 5, where the “B” is the diameter of the largest helix plate; and a minimum spacing no less than 3 FT.
This article reviews the current level of research on the effects of anchor spacing on both tension and compression capacity of helical foundation elements like anchors and piles. The research is on-going, but there is considerable work done by others, plus the current research being conducted by Hubbell Power Systems. The objective is to develop a “generally accepted method of analysis” that is simple to apply to a variety of applications and site conditions.
Terms to Know About Helical Spacing & Capacity
- The center-to-center spacing between helical anchor/pile shafts can be expressed in terms of the horizontal spacing (S) and the diameter of the helix plate (B).
- S/B ratio is the horizontal spacing divided by the helix diameter, which is a dimensionless variable that makes it easy to relate different types and sizes of helical anchors/piles.
- D/B ratio is the vertical depth of the helix plate divided by the helix diameter and is also used to relate different types and sizes of anchors/piles. Both the S/B and the D/B ratios help to compare a wide variety of helix diameters, shaft sizes installed to various depths.
- Group Efficiency is generally expressed as a percentage of the group capacity to the sum of the capacity for an individual anchor/pile of the same size.
Past Helical Spacing Research
Shaheen & Demars (1995)
Interaction of Multiple Helical Earth Anchors Embedded in Granular Soil conducted small-scale model tension tests on in-line anchors and groups. Their results indicate the critical horizontal spacing (S/B) ratio of single-helix anchors in dense sand appears to be > 5.
Lutenegger (2018)
Axial Uplift of Square-Shaft Single-Helix Anchor Group conducted full-scale tension tests on pile groups in both hard and soft clay at the same location. The overburden soils were hard clay, and the soft to firm clays were deeper. The results indicate the critical horizontal spacing (S/B) ratio of single-helix anchors in hard clay appears to be > 4. Likewise, full-scale tension tests on pile groups indicate there is no critical horizontal spacing (S/B) ratio of single-helix anchors in soft to firm clay.
Bradshaw et al. (2022)
Field Study of Group Effects on the Pullout Capacity of “Deep” Helical Piles in Sand conducted full-scale tension tests on pile groups in loose to medium-dense sand. Their results indicate group efficiencies ranging from 60% - 95% for single-helix anchors in loose to medium-dense sand with S/B ratios of 2 – 3.
Present Helical Spacing Research
CHANCE engineers have recently conducted anchor spacing research in both clay and sand soil profiles. The clay site was in Centralia, MO, which has a medium to stiff clay soil for the top seven to ten feet. Full-scale tension tests on in-line anchors indicate the critical horizontal spacing (S/B) ratio of single-helix anchors in medium to stiff clay appears to be > 2. The group efficiency trends from about 89% at S/B of 1 to nearly 100% at S/B of 4. Figure-1 is a plot of the actual group efficiency values as a function of S/B ratio and the associated trendline.
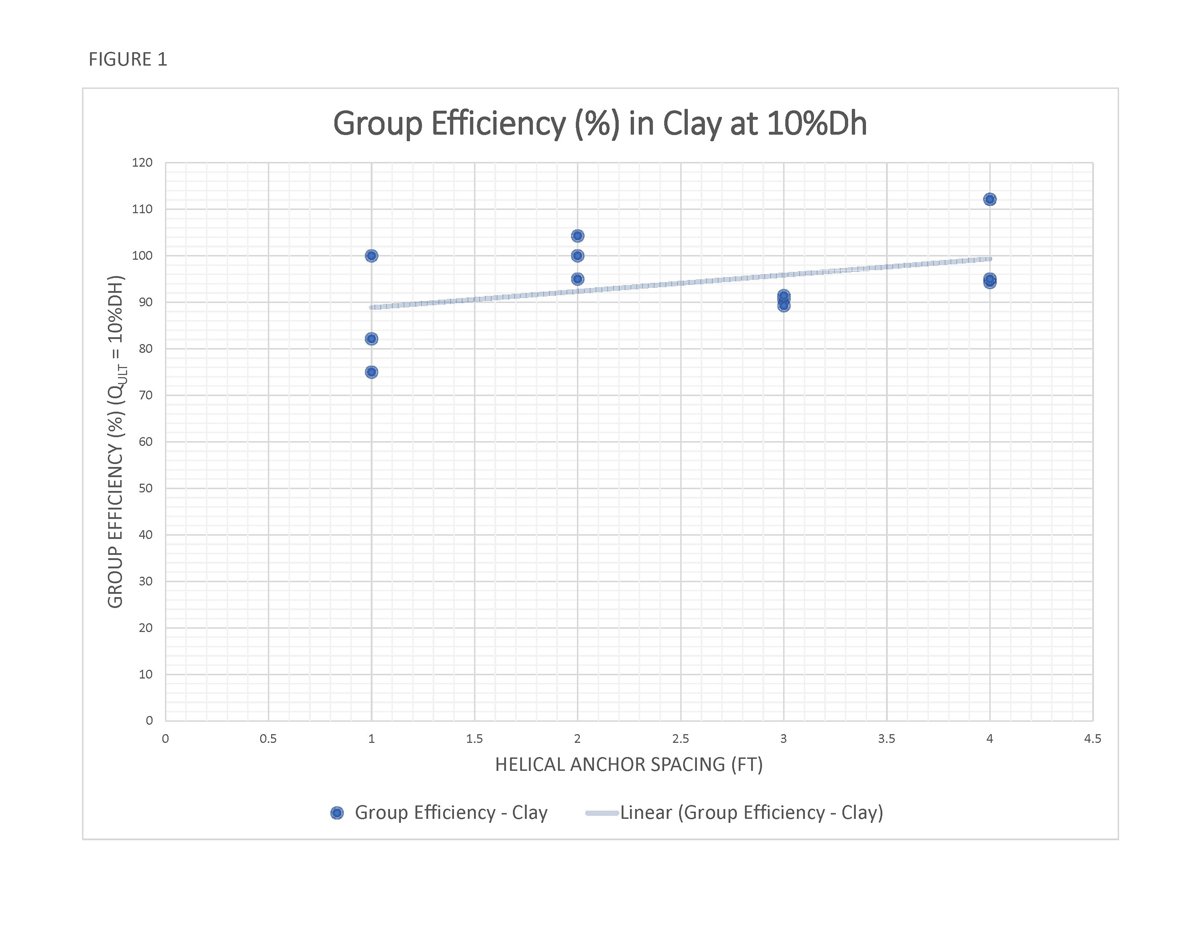
Read more about pile and anchor design methodology in Section 5 of the Civil Technical Design Manual.
The sand site was in Caseyville, IL, which is just east of St. Louis, MO. The test site was loose to medium-dense sand with small cobbles down to depths exceeding 20 feet. Full-scale tension tests on in-line anchors indicate group efficiencies ranging from 50% to nearly 90% for single-helix anchors in the loose to medium-dense sand with S/B ratios of 1, 2, 3, and 4. The critical horizontal spacing (S/B) ratio of single-helix anchors in loose to medium-dense sand appears to be > 3. Figure-2 is a plot of the actual group efficiency values as a function of S/B ratio and the associated trendline. Note there is considerable scatter in the data which make interpretation difficult.
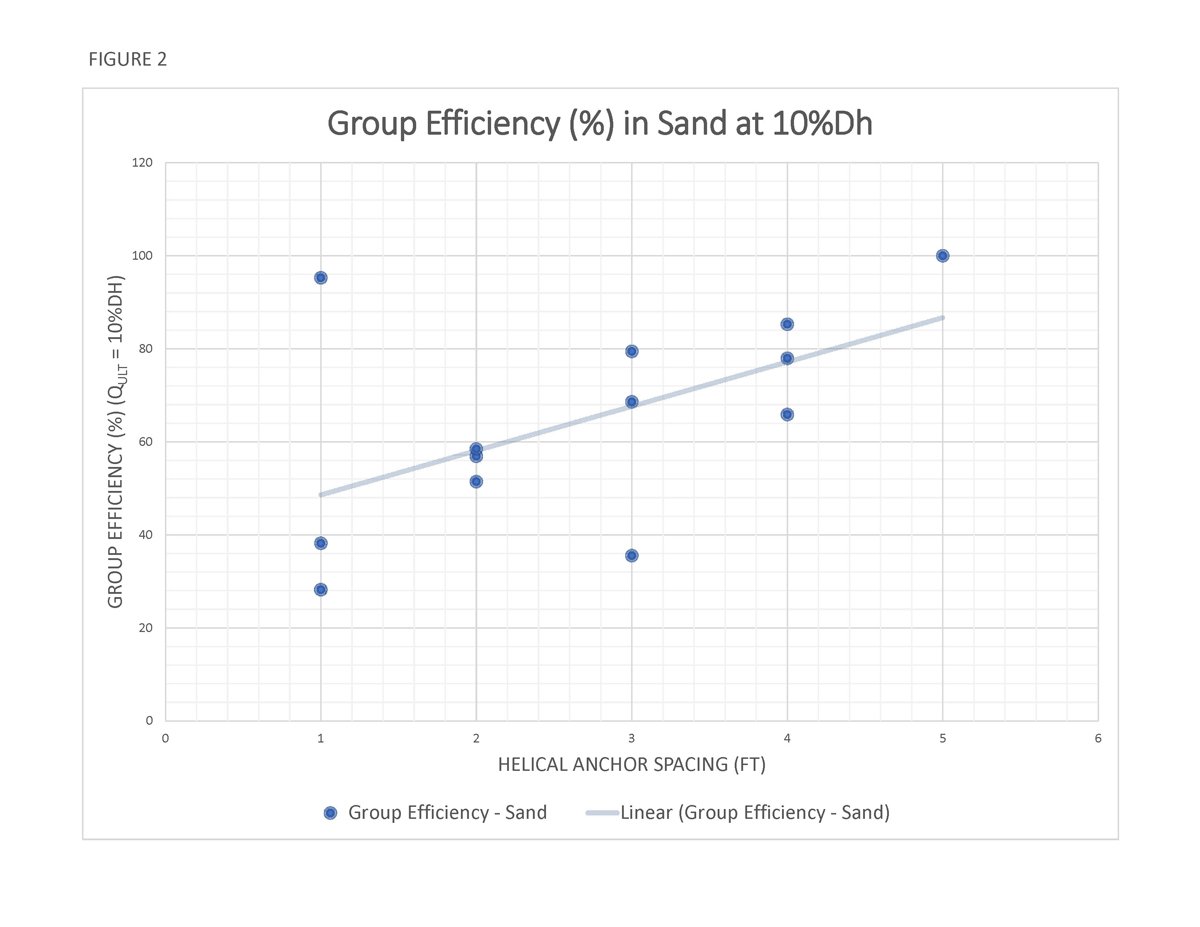
Helical Spacing & Capacity Research Findings
The current and past research generally follows the same trend. Both past and current research confirms that critical horizontal spacing (S/B) ratio is affected by soil type and relative density/consistency:
- Dense sand: requires greater center-to-center spacing to ensure the best group efficiency as evidenced by the need for an (S/B) ratio greater than or equal to 5.
- Loose to medium-dense sand: the critical S/B ratio appears to be closer to 3 based on group efficiency
- Hard clay profiles: require greater center-to-center spacing (≥4) to ensure group efficiencies greater than 90%.
- Medium to stiff clays: allow closer spacing with S/B ratios of 2 to 3 providing 90% to 100% group efficiency.
- Soft clays: There appears to be no critical horizontal spacing in soft clays, meaning the can be spaced right next to each other!
Research is ongoing. Our engineering experts will provide updates as relevant.