Zinc is a common material in plating of ferrous (steel) components. In terms of corrosion protection, how it’s applied can have very different results. Two processes are hot-dip galvanizing (HDG) and thermal diffusion galvanizing (TDG).
Hot-dip Galvanizing
Historically, hardware used in electrical and telephone utility construction utilizes zinc applied by the hot-dip galvanizing process. The level of corrosion protection that results from this process is effective in normal environments and is efficiently applied from a manufacturing standpoint.
HDG steps begin with a thorough cleaning with hydrochloric acid followed by dipping in a molten zinc bath that has been heated to 750 degrees F. Immediately after removal from the zinc bath, a spinning process is used to remove excess galvanizing, followed by quenching, that cools and tempers the coating. With this process zinc adheres to the top layer of ferrous steel. When product with this coating is installed and exposed to the environment, the zinc outer layer is sacrificed as it protects the ferrous metal from corrosion. Over time the zinc layer becomes thinner and eventually protection becomes ineffective and signs of rust start to appear. Rate of zinc deterioration will depend on environmental conditions. Sometimes protection lasts up to 30 years or can be as little as 5.
Thermal Diffusion Galvanizing
From start to finish, zinc applied by the TDG method is vastly different than the HDG process. Following cleaning of the parts by a blasting process as opposed to an acidic solution, the parts, along with a proprietary zinc powder are loaded into a sealed cylindrical oven. At an oven temperature just over 500 degrees F, the zinc mixture changes to vapor. Being soluble in iron, the zinc vapor then diffuses into the surface of ferrous parts. Rotation of the cylinder ensures surfaces are all evenly treated. The volume of the zinc mixture is a precise calculation based on the total surface area of the parts. This results in excellent thickness control and near total consumption of the zinc powder. Once removed from the oven, specially formulated topcoats and sealers are applied, completing the finish.
The basic TDG process, known generically as Sherardizing, has been in existence for over 100 years. Refinements and improvements have occurred over time, leading to the development by Distek NA of the premier ArmorGalv® process in 1993. Hubbell is pleased to offer a variety of pole line hardware products with the ArmorGalv® thermal diffusion galvanizing.
Performance Advantages of Thermal Diffusion Galvanizing
Corrosion Protection
Described above, the TDG process diffuses zinc into the ferrous material, creating a high level of corrosion resistance that exceeds performance of traditional hot-dip galvanizing per ASTM A123 and A-153 galvanizing. The images below compare performance and illustrate the difference between HDG bolts on the left and TDG bolts on right. At the conclusion of 5,000 hours of salt fog testing in a controlled laboratory setting, HDG bolts were virtually unrecognizable, while bolts processed with ArmorGalv® were largely unchanged. Just 500 hours into the test, nuts of the HDG bolts had already seized while the ArmorGalv bolts were fully functional, as if just removed from the box.
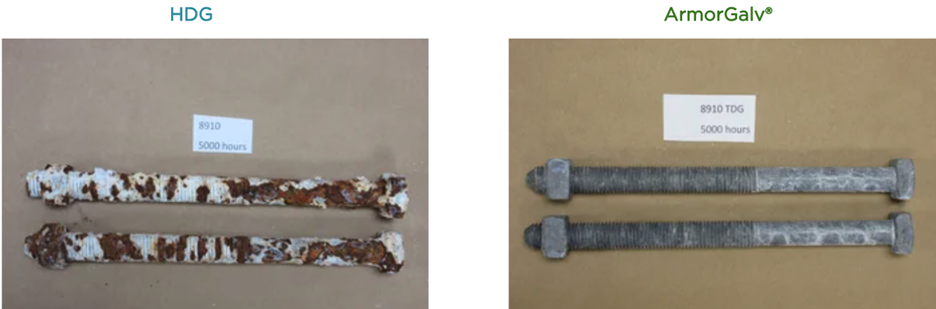
No Flaking, Peeling or Blistering
Approximately 1/3 of the finish thickness is diffused into the surface, effectively becoming part of the component. With TDG there are never surface defects that expose bare, unprotected steel.
Zero Risk of Hydrogen Embrittlement
During the HDG process, it is possible for conditions to be present that cause a decrease in ductility and tensile strength, known as hydrogen embrittlement. TDG presents zero risk of hydrogen embrittlement and ensures integrity of the product.
Uniform Deposition of Coating
TDG coating is uniform. All external and internal features, including crease and threads, receive full coating. This ensures equal protection over the surface of the part. And in contrast to HDG, there is never excess galvanization in threads, so nuts turn freely during installation.
Highly Abrasive Resistant
The zinc-iron alloy layer and a proprietary sequence of topcoats and sealers work to create a product that is highly resistant to abrasion.
Anti-galling Characteristics
Thread galling, that causes nuts to seize on stainless bolts does not occur with TDG, and nuts can be easily removed.
Environmental Advantages of TDG
Eco Friendly
Surface preparation for the TDG process requires no hazardous chemicals and requires little water consumption. Measured emissions are close to zero and the process has been recognized by the EPA with the MVP2 (Most Valuable Pollution Prevention) award for its contribution to pollution prevention. ArmorGalv® TDG is also ROHS, REACH, and PROP 65 compliant.
Cost Advantage of TDG
Short Term vs. Long Term Cost
In the long term, TDG is a significantly more economical solution when compared against the installed cost of frequent HDG material replacements. Line crews can then more efficiently direct their time where needed.
Affordable Alternative to Stainless Steel
Products manufactured from stainless steel are highly effective in solving corrosion issues, but extremely high priced. TDG offers performance that approaches stainless, without the exorbitantly high price.
Demonstrated Performance - Credentials
ArmorGalv TDG is manufactured in compliance with the ASTM A1059/A1059M specification for Zinc Alloy Thermo-Diffusion Coatings. It is approved in use by quality conscious groups such as major utilities, automotive companies and all branches of the US military.
Conclusion
Hubbell offers a variety of pole line hardware products with the ArmorGalv thermal disused galvanized coating to maximize corrosion protection in harsh environments, where hot-dip galvanized products are not effective.
Thermal Diffusion Galvanizing is proven effective and comparable to stainless with performance, cost and environmental advantages over Hot-Dip Galvanizing.