There is no better way to guarantee the capacity of a pile than to conduct a load test. While torque-to-capacity ratio (Kt) in conjunction with bearing capacity calculations will result in 0.3% of piles that are inadequate (that is 3 in 1000), the only way to 100% guarantee a pile will carry the load is with a load test.
Instances that may require a test
There are many reasons why a load test might be required for a project. A few examples include when:
-
-
-
A pile refuses on a dense layer
-
A larger than default (site specific) Kt is desired
-
Soil information is lacking or unknown
-
The project engineer requires one.
If the pile met refusal on rock or dense soil layer, but did not reach the required torque, the pile may still have the compression capacity required. A load test can determine if installing to refusal will result in the required axial capacity.
Some sites will have higher Kt values than the published default values. If a location is known to have Kt values that are 15 for example (typically 10 is the recommended value for CHANCE® Type SS helical piles without a load test), a load test can allow for lower installation torque and less embedment depth.
Lastly, if there are lots of piles on a job, an engineer may just specify a test pile for peace of mind. When using more than 50 piles on a job, testing at least one pile is typically recommended to ensure there are no issues.
Tension Vs. Compression
When testing a helical pile, it will always be more cost effective and easier to test in tension rather than compression. This has to do with the fact that when pushed on, the earth gives more resistance than the sky. A tension test applies the load back into the ground (typically through large mats); whereas, a compression test pushes down on the pile and thus requires installing reaction anchors to pull on. Instead of installing one pile for a tension test, at least 5 (single test pile and four reaction anchors) have to be installed for a compression test. Whenever possible, an engineer or contractor should consider conducting a tension test even when the helical piles will be used for a compression application. The logic is a tension test will result in a lower capacity compared to compression because the soil is slightly disturbed by the helices passing through it and soils typically get denser with depth. There are times when a compression test is essential (for example, when a compression pile refuses on rock or the soil profile shows stringers of dense and loose soil at bearing depths); but if possible, a tension test is a much more cost-effective option.
Read about what happened in a difficult compression test rural Brazil!
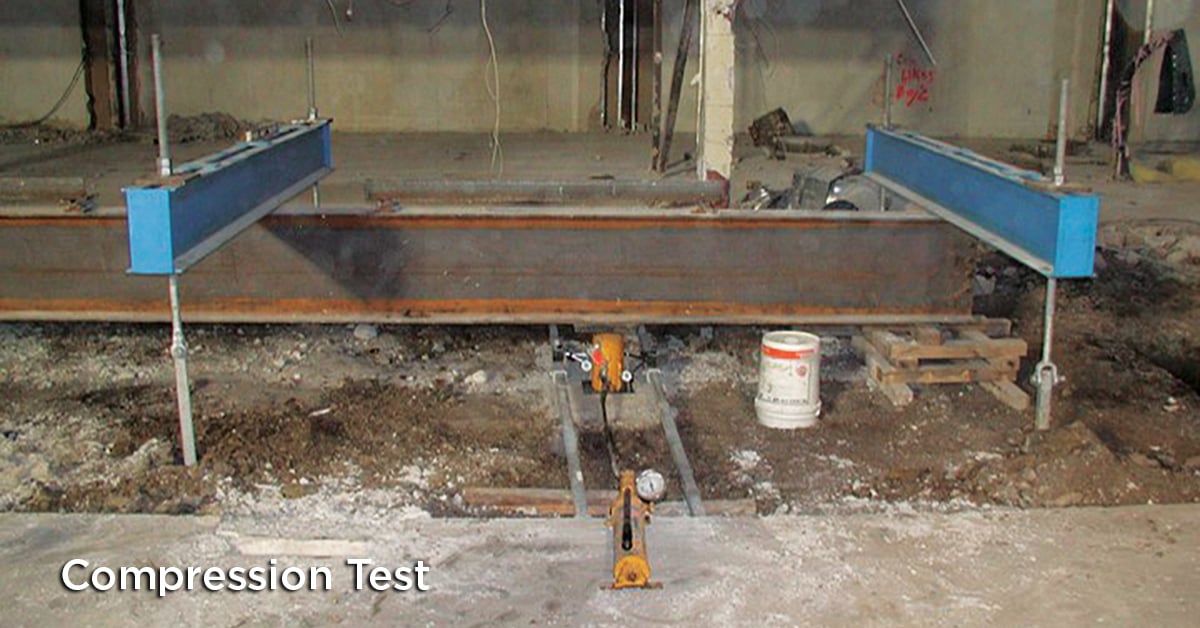
Conducting a load test
Load tests are typically conducted using the applicable standard for either compression (ASTM D1143) or tension (ASTM D3689). The specification calls out multiple types of tests, but the most common is the Quick Test. In the Quick Test, the load increments are between 5% and 10% of the anticipated failure load of the pile. The increments are held for a minimum of 4 minutes. During these 4-minute hold periods, the load is held constant. This may require additional pumping of the hydraulic jack due to creep to maintain a constant load for the hold period. The deflection value recorded at the end of the hold period is the displacement for that given load increment. The load is then increased, and the same procedure repeated. This is typically done until the pile has displaced between 2 and 3 inches. After the pile has reached the maximum test load, it is common to measure the rebound of the pile with around 4 load decrements.
Interpreting a load test
After the load test is completed, it is time to determine the ultimate capacity of the pile. Hubbell Power Systems, Inc. recommends using a 10% offset failure criterion. This means that when the helix plates have displaced 10% of their average diameter (net deflection), the ultimate capacity of the pile has been reached. One thing to note is that the net deflection (helix movement) is only part of the gross deflection (pile cap movement). The elastic lengthening or shortening of the shaft is also part of the gross deflection as is any coupling slack in the pile. As can be seen from the load test below, the pile reaches failure when it crosses the PL/AE + 0.1 Davg line (Around 64 kips in plot). One thing to note about this plot in particular, is that anytime you see something like the jump circled in red, it is probably due to slack in the pile connections. Since lead sections and extensions are bolted together, there will be some amount of “give” in each connection. The typical net deflection at working loads (typically ½ the ultimate capacity found with the 10% offset) will be between ¼” and ½”.
The owner or structural engineer usually determine the amount of gross deflection allowed for a given load. This should be specified before the pile is designed and the test is conducted. Limiting total gross deflections to between 1 inch and 1-1/2 inches is typical at ultimate geotechnical capacity.
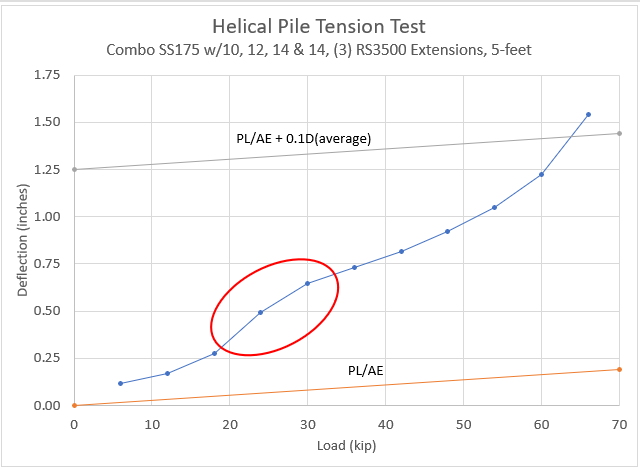
Learn more about load testing
Learn more about load tests in this article: 5 Questions About Load Tests on Helical Piles [Answered] or to get more in depth, check out Appendix B of the Chance Technical Design Manual.