Chance helical piles have been evaluated and have gained acceptance as building-code-approved products for seismic design categories D, E, & F. Following is a case study of a seismic zone foundation built on Chance helical piles.
The proposed expansion of the BoDean Company Asphalt Plant, located on two acres in Santa Rosa, California, is surrounded by residential neighborhoods. Three new 14’ diameter batch silos and conveyor equipment rise more than 85’ above the 40’ x 60’ foundation pad and can contain 900 tons of bituminous material batched at 300° F. RGH Geotechnical Consultants assigned the project to Site Class D with ground acceleration parameters Ss= 1.85g and S1= 0.72g. Given the small footprint, a single boring indicated highly variable alluvial deposits and that “the site is underlain by interbedded soft to very stiff clay and loose to very dense gravel and sand”. Two thin layers of liquefiable materials were identified at depths of 7 and 15 feet below grade and groundwater was encountered at about 10 feet. The initial foundation design, prepared by the silo manufacturers, was a 5’-6” thick monolithic slab intended to counteract the high overturning reactions. Differential settlement across the 40’ dimension of the pad was estimated to be as much as 5” and was deemed unacceptable by the Santa Rosa Building Dept. for this seismic zone.
Travis Whitted, Geotechnical Engineer and Vice President of RGH Consultants recommended a deep foundation system to overcome the differential settlement problem. Driven piles were not an option in this neighborhood and drilled cast in place piles were rejected due to the high water table, potential caving soils and low skin friction values. Helical piles provided the flexibility to deal with the variable conditions, eliminated off-haul of spoils and provided direct feedback (continuous monitoring of installation torque) that each pile would perform as designed with minimal proof testing of production piles.
A SEISMIC SOLUTION
Jeff Martin of Steelhead Engineering designed the revised foundation. He explains, “The added cost of a deep foundation is never easy for a client to accept. BoDean was willing to make the investment but wanted a value engineered solution. Fortunately, the consolidation was expected to occur in the upper 15’ and the liquefiable layers were thin so slender piles were our most cost effective option. Using helical piles we were able to achieve the required capacities at whatever depth we encountered dense enough soil. Strikingly, even across this 40’ x 60’ pad installed lengths varied between 25’ and 75’. The cost of the piles was partially offset by drastically reducing the volume of concrete and excavation.”
The deep foundation system incorporated 144 CHANCE® SS175 helical piles installed to a minimum torque of 8,500 foot-pounds for an allowable load of 42 kips (ultimate 84 kips) per pile. The high loads required tight spacing so the square shaft piles were slightly battered to maintain minimum required spacing between the lead sections at depth.
BoDean’s owner Dean Soiland and Chief of Operations Charlie Young visited the offices of Maloney Construction Inc. to observe the installation of a typical helical pile prior to accepting the new design. Sean Maloney, the president of Maloney Construction was happy to demonstrate the installation. “Dean and Charlie came over to my yard and watched us install a helical pile. We showed them how the pile are installed, how they work, and how we continuously monitor the torque,” explains Maloney. The men were satisfied and the project went ahead.
PILE INSTALLATION
Installing the piles and terminations was accomplished in less than a month.
Each helical pile had a minimum 8”, 10” and 12” helix lead while several had one or two additional 14” helices depending on the conditions at each location. The pile terminations were only 15” apart in many locations and so were installed at a 3° to 6° batter to maintain adequate spacing of the lead sections. A John Deere 120 excavator with a 12,000-ft.lb-torque motor was used for installation.
“Just to show how variable the soil conditions really were, a few piles reached torque requirements at 25 feet–others at 75 feet,” says Maloney. “As we drive the piles, we record the torque every foot with a strain gage based torque monitor to make sure that we have the required embedment and torque before we call the pile good,” explains Maloney.
Learn more about torque testing in helical pile design.
Since the required quantity of CHANCE SS175 extensions was unknown, timely resupplying was critical and a close working relationship with their local CHANCE distributor.
Each helical pier was terminated with a DYWIDAG adapter and 150 ksi rope thread bar to allow for a positive mechanical connection to the back-to-back channels that were used as primary reinforcing steel and the 1-1/4” anchor rods specified by the silo manufacturer. Concrete volume was minimized by utilizing Geofoam blocks to create a waffle slab with a 12” minimum slab thickness and an overall maximum depth of 2’-6” at the integral grade beams.
Maloney Construction specializes in CHANCE helical pile systems primarily for foundations and retaining walls. The company has been in business for 18 years and has installed CHANCE helical piles at over 300 sites.
TESTED AND PROVEN
On August 24, 2014 at 3:20 a.m., with the batching silos empty, a magnitude 6 earthquake struck American Canyon approximately 30 miles southwest of Santa Rosa. Peak ground acceleration measured nearest the site was moderate and peak ground velocity was strong. BoDean reported no damage or visible movement of the foundation relative to adjacent paving. Security video from that time taken from the single story wood framed control shack clearly showed ground motion while video taken from the top of the silo structure did not.
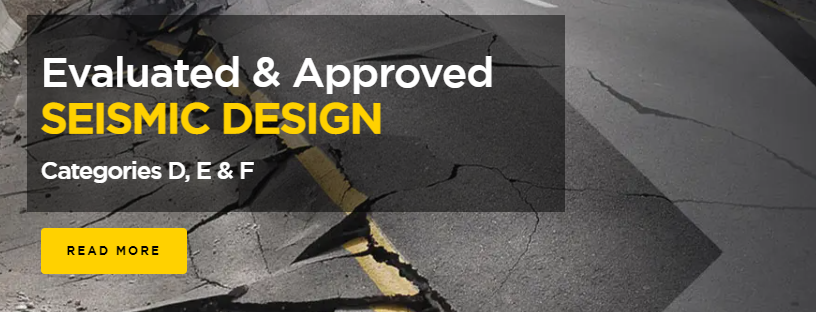