One Richmond Row, a 32-storey apartment tower rising in London, Ont., will soon be the tallest building on helical piles in North America. The project site at 517 Richmond St. is in the middle of a city block in a desirable area of downtown London. That was one of the developer’s main selling points to potential renters of its one-bedroom and two-bedroom suites, who will be “immersed in the culture and excitement of a thriving city centre.”
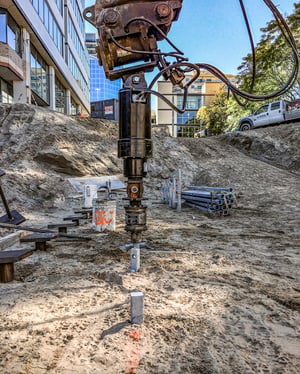
The site presented the project’s structural engineers with particular challenges, including its high water table and deep deposits of sand material as well as close proximity to surrounding buildings and its restricted street access. Although the initial geotechnical report recommended driven piles or caissons to support the proposed 32-storey tower, driven piles were considered unfeasible because of the potential damage to nearby structures due to vibration and the disruption installation would cause in the city’s core. Caissons would have come with their own challenges – long construction time, substantial traffic control plans and, most importantly, costs – that would have made the project economically unviable.
Structural engineers explored all the options to give their client the best, most efficient and most economical design, says Brian Huber, project manager for Chance distributor EBS Geostructural of Breslau, Ont. EBS has specialized in micropiles and helical piles for almost 20 years and is the Ontario distributor and main installer of Chance helical piles, which are manufactured in Centralia, Mo., by Chance Foundation Solutions, now a division of Hubbell Incorporated.
The proposed tower’s location, which previously had a one-storey commercial building and a parking garage on it, was already owned by Old Oak Properties.
“From a cost perspective it made more sense for the developer to demolish existing buildings on the site than find a new vacant site elsewhere,” said Huber, who notes that many of the logistical challenges that caisson installation would have posed for this restricted-access downtown site were eliminated by using helical piles; including the need for access and egress for drill rig equipment, dump trucks removing spoils, the ready-mix trucks delivering concrete and the need for laydown areas for rebar cages."
CLICK TO READ THE REST OF THE ARTICLE FROM PILING CANADA
or Download a PDF of this article.
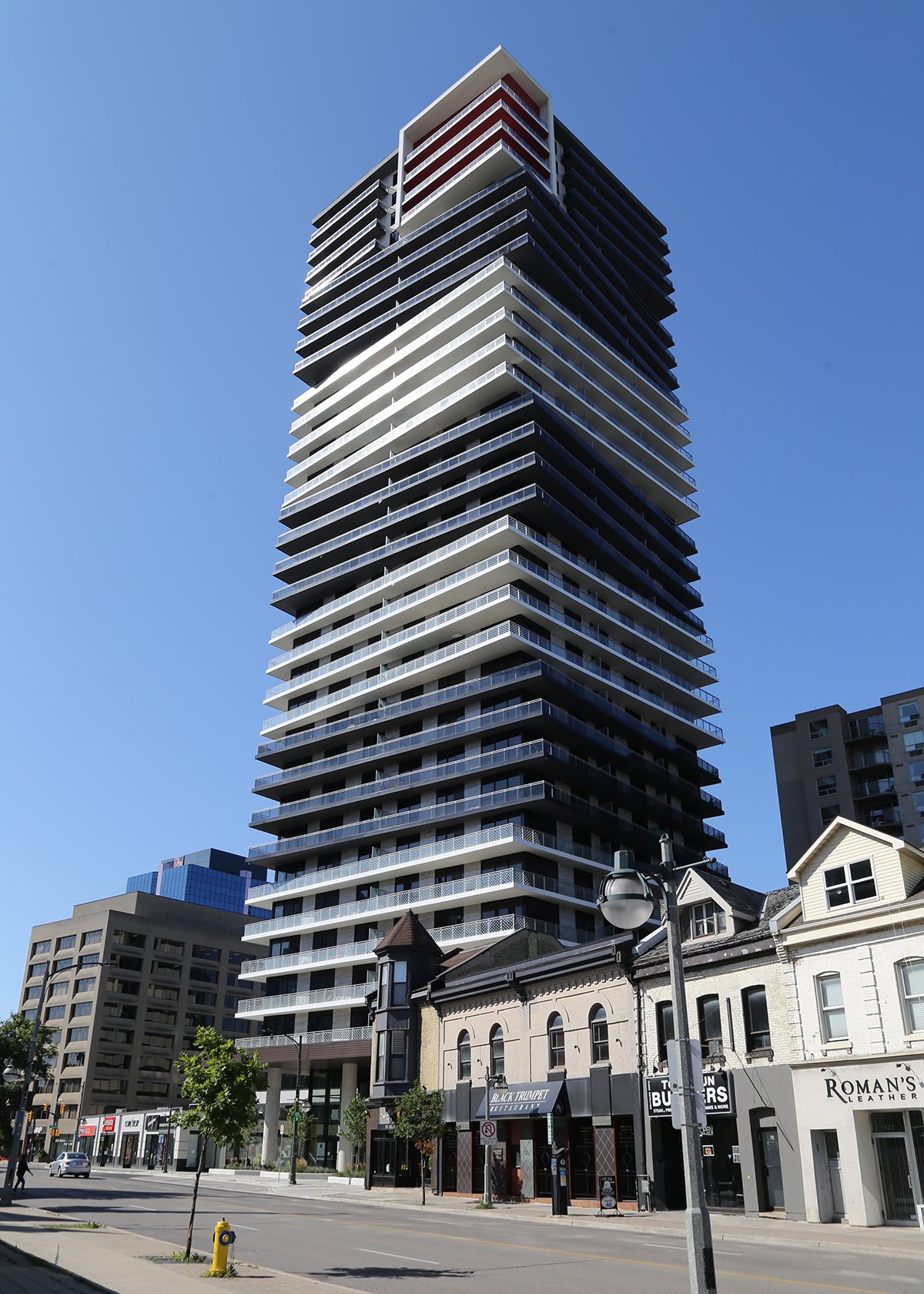