This high-end home was constructed in loose, sandy soil with a high-water table, requiring a deep foundation system whose capacity could be field verified. Soil borings reported loose sandy soils above dense sand layers with the water table at 3 feet.
Engineers considered both helical piles and driven concrete piles for the job. Both technologies are good choices when unstable overburden is a factor. They both are installed until their tips reach load-bearing soil before being attached to the structure via a pile cap. However, there are key differences in how the two technologies are installed that give helical piles the clear advantage in this situation. These are the reasons that the engineers and contractors decided that helical piles were the best foundation solution for this project:
-
-
-
Low mobilization cost – Chance® helical piles are sold by a local distributor and are easy to transport even to limited access jobsites
-
Small installation equipment – a Cat® 308 Mini Excavator with a Digga 12K drivehead was all that was required for the foundation installation
-
Minimal disturbance during construction - no vibrations or hammering – Unlike driven piles which are hammered into the ground, helical piles are screwed into the ground using the mini excavator’s torque motor.
-
No spoils – driven piles require excavation and soil removal from the jobsite, but helical piles cause very minimal disturbance to the ground and do not require excavation before installation
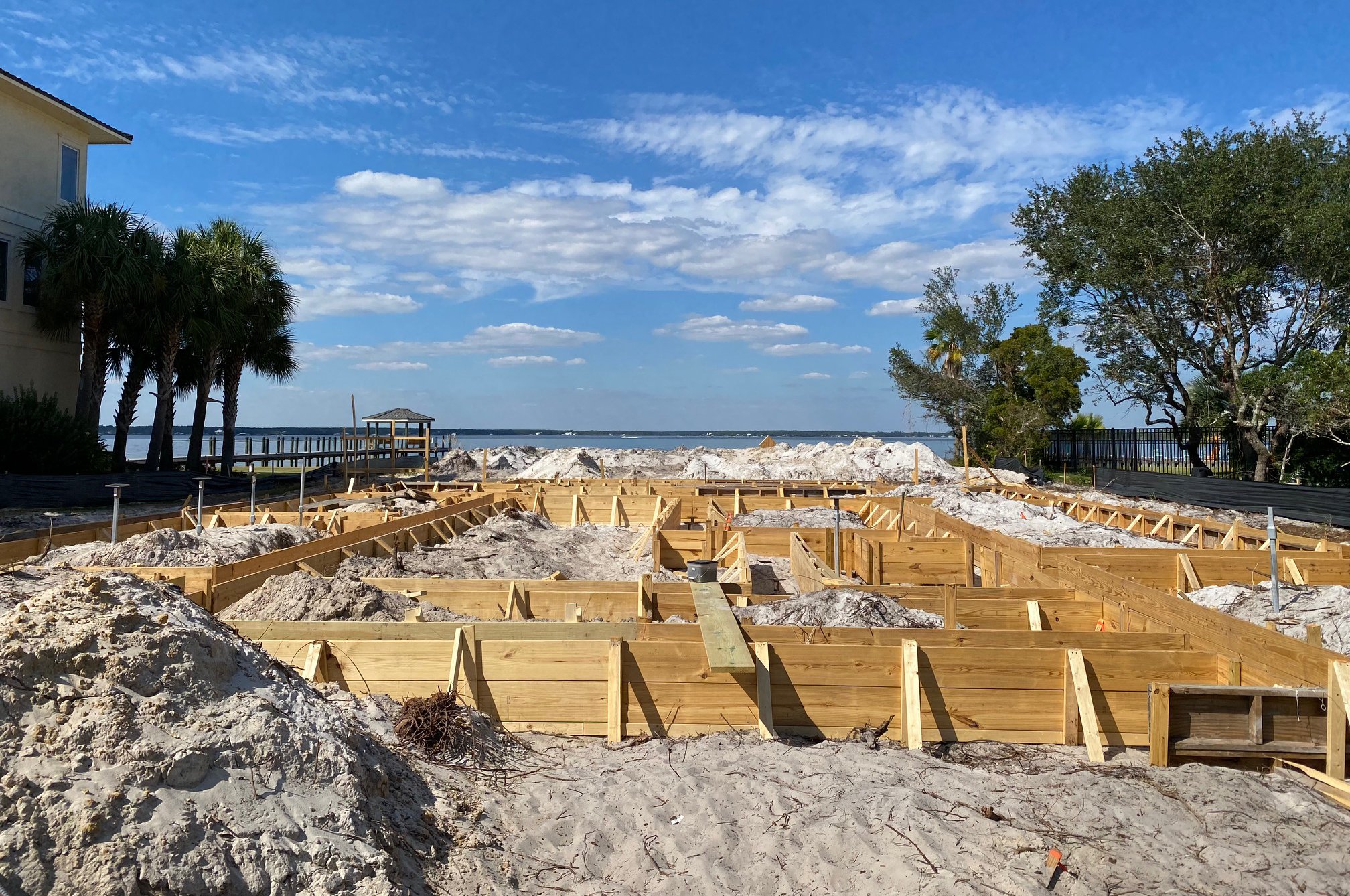
Since the house was being constructed in a heavily congested neighborhood with houses on each side, the vibrations caused by driven piles were not acceptable.
Therefore, the general contractors, Vlahos, DeBogory & Tuck, who specialize in top-quality, custom-built homes called on Mason Grady Foundations to install a Chance helical pile foundation on this challenging jobsite.
Engineers at Foundation Technologies, Inc, the Chance helical pile distributor for the region, used engineering design software, HeliCAP v3.0, to recommend a helical pile that could achieve the required load (100-kips ultimate compression and 50-kips allowable compression working load) at 25-30’ tip depth.
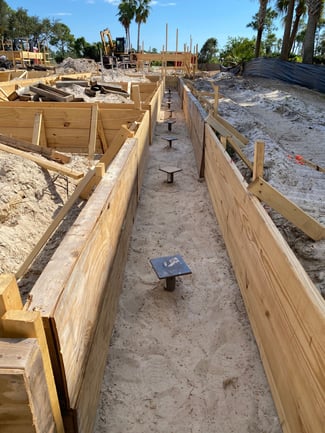
The Mason Grady team installed 144 helical piles in 9 days. The team from Vlahos, DeBogory & Tuck was impressed with the speed of install and appreciated no messy cleanup and no disturbance to existing structures nearby.
Torque was monitored during installation using a Chance Digital Wireless Torque Indicator. Because there is a direct correlation between installation torque and capacity, installers could confirm the capacity that the engineers had calculated for each helical pile. Additionally, a field technician with Foundation Technologies conducted a load test prior to installation of the production piles so the general contractor could proceed constructing the residence with complete assurance in the foundation. The Chance SS175 helical piles surpassed the desired load and deflection acceptance criteria.
Read more – 3 Methods to Determine Helical Pile Capacity (and why you should use 2)
To learn more about how Chance® Helical Piles can save you time and peace of mind on your next coastal project, contact your local distributor.
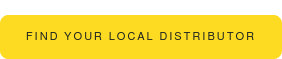
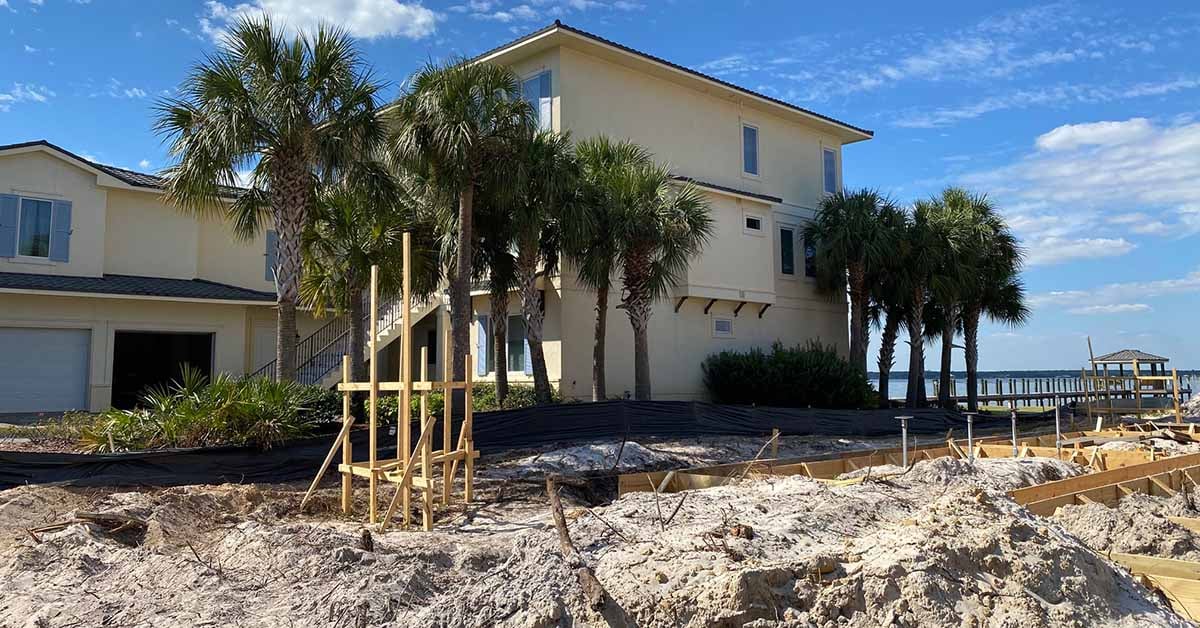