There are many options when it comes to temporary shoring: the support of soil that would otherwise be in danger of collapsing during an excavation. Some common methods include:
-
-
Trench Boxes – consists of 2 plates held apart by spreaders; the parts are welded together and braced firmly against the side of an excavation to prevent collapse
-
Soldier Piles & Lagging – a steel H pile frame is drilled or driven around the perimeter of an excavation and covered with lagging sheets to support the lateral earth pressure load
-
Sheet Pile Walls – consist of interlocking panels that form a wall around the excavation; may require the addition of helical anchors for additional lateral support
-
Tie-Back Anchors – although CHANCE provides solid steel tieback screw anchors, this method is often done using grouted tendons, or cable strands, to hold soil back. The anchorage is attached to structural facing elements and tensioned.
-
Helical Soil Nails – also known as soil screw anchors, these consist of 1.5-inch square solid steel shafts, on which steel bearing plates or helices are welded at regular intervals. They screw into the soil and obtain their bond with the soil through the bearing of the helices against the soil. Disambiguation: Soil Nails with no helix must be encased in a grout column.
Nailing it down – Tie-Back Anchors vs Helical Soil Nails
Both soil nail walls and tieback walls can be constructed with helical anchors. Although they may seem similar on the surface, they are actually very different solutions.
Tieback Wall - constructed by placing structural facing elements, typically steel soldier beams, vertically, or near vertically, at the face of the wall to be constructed. The facing system is anchored to the earth using very high-strength steel tendons or anchorages. The design of a tieback wall requires that the wall facing be structurally stiff enough to retain the earth without excessive deformation. Likewise, the anchors need to be installed deep enough and need to be tensioned to a high enough load to be able to support the facing without creep of the anchors with time. Anchors are spaced as far apart as the stiffness of the facing will allow. The design also requires that the facing element be embedded a sufficient depth to mobilize the passive resistance of the soil to resist facing movement at the toe of the wall during and after construction. The structural facing is “pre-loaded” when the anchors are tensioned. The length of the tieback anchors will vary based on their position in the wall, the soil type/strength, and the wall height. Watch a video about helical tieback anchors.
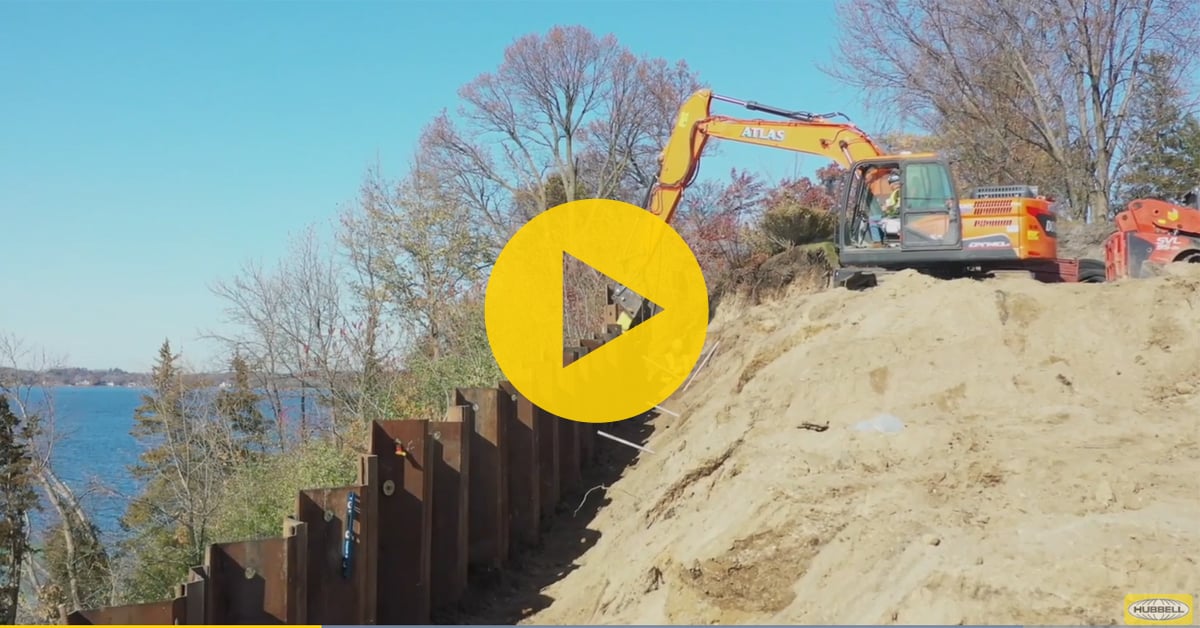
Soil Screw Wall – steel reinforcing elements that are not tensioned. They are passive soil reinforcements that are placed in sufficient quantities within the soil to create a coherent gravity mass. The soil screws, also known as helical soil nails, have a lower load requirement than tieback anchors, and are placed closer together, typically on the order of 5 foot on center (i.e., 4 to 8 soil nails typically replace one tieback). The soil screws are normally of a uniform length, with the actual length on the order of 70 to 100 percent of the wall height, depending on the soil strength and surcharge conditions. The objective of helical soil nailing is to create a reinforced soil mass that has sufficient internal stability and size so that it can provide sufficient safety factors against movement due to sliding, bearing failure, or global instability. The objective of the facing is to retain soil and to provide enough structural capacity to ensure that the nail head will not shear through the facing and that the facing will not fail in flexure between nails. Watch a video about soil screws.
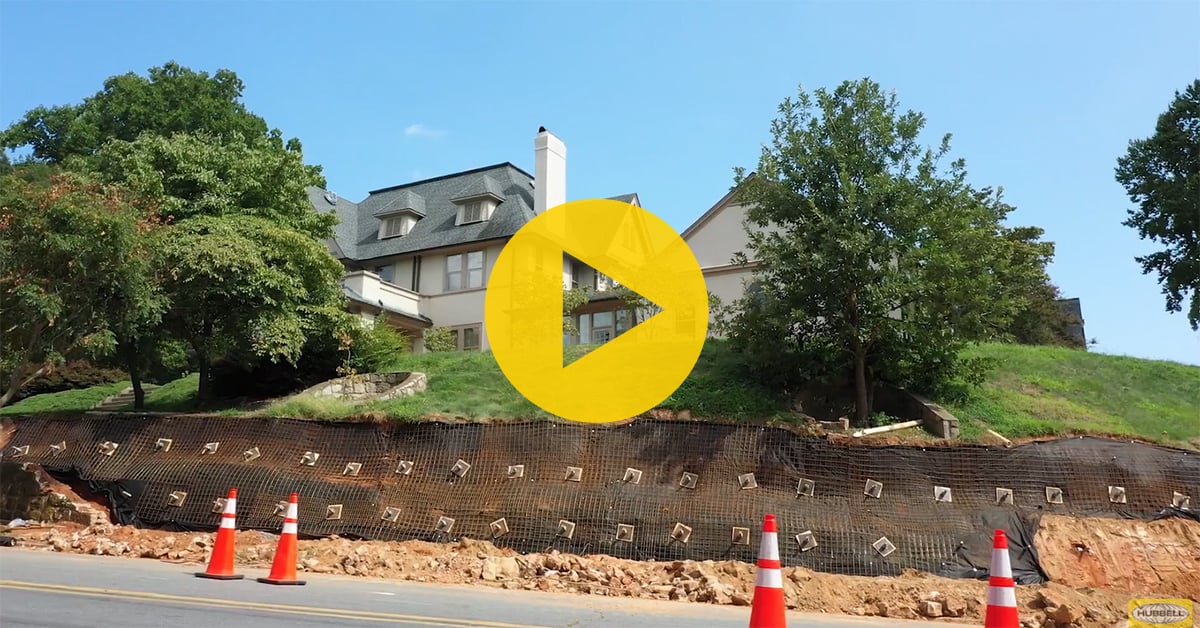
Case Study – Temporary Shoring for Heavy Equipment Installation
A company that manufactures corrugated cardboard needed to install a new conveyer pit inside their factory. The pit size was 140 feet long x 22 feet wide x 12 deep – over 3,000 square feet. Since the pit was inside an existing building with limited headroom and support columns adjacent to the installation space, it needed to be stabilized so construction could proceed safely with temporary structural support.
The CHANCE soil screw system was chosen for the earth retention project due to its speed of installation and can be done in low headroom interior applications while working around existing structural columns.
Stable Foundations proposed using a soil nail system utilizing CHANCE "Soil Screws" and shotcrete as a shoring system. This temporary shoring system provided safe access for workers to build the pit.
The existing building had height restrictions making it difficult to get larger equipment inside the building. Soil Screws can be installed with smaller excavation equipment and grout pumps, making it an ideal choice over competing technologies.
In addition to the benefit of installation in low headroom conditions, the installation method caused no vibration to the existing columns adjacent to the shoring needed to be supported. CHANCE Underpinning Brackets provided support to the columns since they were so close to the excavation.
The soil boring data showed sandy clay in the 8-12 Nspt blow count range. Armed with this data, HeliCAP® helical capacity design software along with SnailPLUS Soil Nailing Software were used by engineers at Master Engineers to determine anchor quantities and lengths based on the soil and required depth to get the new pit installed, providing a system that could be constructed with predictable capacity.
Over 8 days, 246 soil screws were installed using a Kubota KX080 Excavator with a 10k Digga Drive Head. The soil screws used were 10-12 feet long depending on the design shore height. On the columns, (10) CHANCE C150-0121 Underpinning Brackets were used in conjunction with CHANCE SS5 square shaft helical piles with a 3-helix lead section (10/12/14) installed to a depth of 21 feet.
As part of the tooling equipment, a CHANCE Digital Torque Indicator provided real-time torque data during the installation, making it easy to confirm the required 1900 Ft-lbs minimum torque. The tension capacity required was 19 kips with a working load of 12 kips.
With CHANCE Soil Screws you can begin the temporary shoring process on day one. Other systems usually require perimeter piles to be done before top-to-bottom excavation/shoring can begin. Find your local distributor if you would like to learn more about the benefits of soil nailing or tieback walls for your next shoring project.
Walder Foundation Products is the CHANCE distributor for Virginia. Headquartered near Richmond, their certified foundation repair installers have performed more than 7,000 residential and commercial projects.