Here are a few facts you may not have realized until now…
Electric lines are blamed for 9% of wildfires
5 to 10 arc-flash explosions occur in electrical equipment daily within the U.S
….. these numbers all relate to one subject: Reliability
Reliability has been a sizzling topic of discussion in the U.S and across the globe for several years. It is by nature a broad topic which by nature that is difficult to address and can be approached by many angles. SAIFI, SAIDI, CAIDI, MAIFI reliability indices are in place as a way to measure distribution system reliability. They provide a comparison basis for electric utilities regarding the quantity and quality of electricity delivered to consumers. Indices are also now frequently used as the key to unlocking and improving the performance of underperforming feeders.
How to identify and track worst-performing circuits?
Methods for identifying and gathering information to generate worst-performing circuit programs have traditionally relied on feeders’ trend performance or historical data relating to customers that have experienced sustained outages. This is where reliability indices are used.
However, there is one caveat to selecting troublesome circuits based on indices only: there is no standard description available of how poor the indices need to be before action is required. For example, is second quartile performance unacceptable? At what point do we start moving feeders to the worst performing circuits (WPCs) list?
As a result, most Public Utility Commissions (PUCs) have taken action and now require electric utilities to develop a methodology to report their Worst-Performing Circuits (WPC). They are asked to submit a quarterly action plan with the goal of improving WPCs to avoid penalties.
A successful reliability program starts with the careful selection of your worst feeders
The identification and tracking of poor performing circuits usually wind up in the process of having crews patrol the overhead distribution lines and look for both visible and non-visible causes of flickering lights or power outages. They also look for failing devices that may require replacement or repair, and other noticeable indicators.
CLICK HERE TO DOWNLOAD THE APPLICATION GUIDE ON HOW TO IDENTIFY AND MONITOR YOUR WORST PERFORMING FEEDERS
However, while aging equipment might be the obvious reasons behind a poor performing circuit, as Thomas Short pointed out in in the Electric Power Distribution handbook, even “good” or well-performing circuits can show signs of poor performance over a 10-year span and end up on the worst 5% list.
So…………………………………………………
If we can’t rely solely on reliability indices. Deploying engineering crews is both time-consuming and expensive and provides only a limited view in identifying these underperforming circuits.
What is the solution to improving reliability when under time, resource and budgetary constraints?
With a short installation time – 20 minutes or less with hot stick – smart grid line sensors detect all events and faults on circuits and provide that information directly to the SCADA system or proprietary software. This allows you to continuously identify, monitor and track your worst performing circuits.
The information can easily be shared with the engineering team and distribution operators to proactively identify problematic circuits and track trends. It also allows you to develop and implement a proactive recovery plan prior to the “good” circuits being added to the WPC report.
In this section, we’ll show you how smart grid line sensors, together with powerful software, can help you:
- Identify and prioritize your worst-performing circuit on the distribution network
- Help generate targeted reliability programs to improve performance
- Manage your operations and maintenance (O&M) budgets more efficiently
1. Identify arcing equipment early on!
Did you know that five to ten arc flash explosions occur in electric equipment daily within the United States? Damaged, poorly maintained or aging equipment is often the most common cause of arcing, especially on the distribution networks. Electric arc faults can occur because of short circuits, damaged insulators or corroded equipment.
An arc flash can produce a tremendous amount of energy that can lead to fires and explosions and cause a safety hazard that can result in serious injuries or even death for electrical engineers or bystanders.
Such dangers can be prevented and here’s how. When equipment is about to fail or arc, it generates a series of what we call line disturbances. These are short-lived fault events that don’t trip standard grid protection and usually remain unseen by SCADA systems. Line disturbances are tell-tale signs that something potentially serious is happening, which only a grid monitoring platform with smart grid sensors is able to detect.
2. Detect Dipping, Sagging, Slapping or Slacking overhead conductors
Overhead conductors must be kept within safe tension parameters. If the conductors are too stretched out between supports, the stress in the electric wire may, in certain cases, break the support structures due to excessive tension. Strict standards are in place to determine what the “correct sag “should be. Anchor guys, also known as a guy wire, are also used to anchor the poles and add stability to relieve stress on the system. But over time, equipment tears (Anchor guys fo, for example,n degrade over time especially in areas where large cattle rub up against them.) coupled with ice or high winds, can increase the forces on the system and cause the conductor to become increasingly looser
Ensuring and maintaining the correct and safe tension is a careful balance utility companies have to deal with constantly. In addition to the mentioned causes for sagging lines, they also have to take into consideration issues such as thermal expansion and contraction. For instance, power lines that are subjected to current overloading conditions can heat up and expand. This can also cause them to slacken and hang lower. This latter phenomenon is very common during summer months as additional demand for electricity increase due to the use of HVAC equipment.
Slacking overhead power lines can have drastic impacts and even fatal consequences:
- Conductor slapping – During windy conditions, if power lines are too loose they can swing and clash with each other.
- Blackouts – In worst cases, sagging lines can cause major power outages or even blackouts. One of the most prominent examples of this was a blackout in 2003. A contributing factor for this was an overhead line that was situated too close to trees. This event was reported as the “largest blackout in North American history” and left almost 50 million people in the northeastern U.S. and parts of Canada without power.Bryan Walsh in a Time magazine article wrote:
“It was the largest blackout in North American history — and five years later, with the grid sagging again under the weight of increased energy demand, there’s no guarantee that we won’t see another outage.”
Read the following story to learn how line sensors can help you avoid risks of blackouts and brownouts.
Sagging lines were not the only cause of this blackout. There was another culprit as reported in the same article: “It started with a tree in need of a trim… When the line sagged too close to the tree, it faulted and tripped off-line”, which leads us to the third reason why you should invest in line sensors to prevent your feeders from ending up on worst-performing lists and improve circuit reliability.
3. Implement targeted tree trimming activities
Utilities around the world spend millions each year trimming and cutting down trees that can interfere with power lines. Trees and vegetation growing into, or near overhead power lines can create serious safety and service reliability issues. So, in recent years, utilities have put in place targeted tree and vegetation maintenance plans as part of their worst performing circuits programs to maintain the operational efficiency of overhead distribution lines.
Here is how trees and vegetation impact distribution network operations:
Trees and vegetation largely impact reliability indices
As pointed out in an Energy Central article, for many utilities, trees are the number one cause of unplanned distribution outages. Tree-related power outages commonly include 20 percent to 50 percent of all unplanned distribution outages. A utility vegetation management report issued by the U.S federal energy regulatory commission confirms the fact that “the single largest cause of electric power outages occurs when trees, or portions of trees, grow or fall into overhead power lines”. In the Distribution Reliability and Power Quality book, the author exemplifies how Duke Power discovered that trees caused 35% to 50% of the circuit breaker and recloser lockouts.
With most faults on overhead lines resulting from natural causes such as vegetation growth, it’s clear that falling trees have the most impact on customer minutes interruption (CMI) when compared to other causes of power outages.
Trees + vegetation + wire lines = Safety Hazard
Areas with high vegetation density are typically constructed using “tree wire.” Conductors are covered with a layer of insulation to prevent electrification of anything that may come into contact with it. But this type of insulation can rub away over time. If trees and branches brush up against exposed wires, it can act as an electric conductor. This is particularly dangerous during times of heavy rainfall or storms and can potentially lead to serious injuries for engineers and become a serious public safety issue. This is why tree trimming and vegetation maintenance programs are particularly important when carrying out risk assessments and for preventing power outages.
A NY Times article –Fires’ Toll Rises as Power Lines Come Under Scrutiny ‒ described that
“electricity can arc between a line and another object, like a tree limb, when they touch or come close to each other and drop sparks onto the grass, twigs and leaves below”. In the same article, Daniel Berlant, a California Fire spokesman, said that “…in the last three years, in all the wildfires for which the department has determined a cause, electric lines were to blame for 9 percent, most often as a result of contact with trees,”
Furthermore, the combination of dry bushes, trees, and power lines can often lead to fires which directly impact the interest of public safety. That is a growing concern and challenge faced by electric utilities today. Such conditions – especially in dry regions such as California which has been fighting droughts for the last 5 years – can quickly spark a fire and have devastating effects as illustrated too often in the news:
- Associated Press: Sparks from electric power lines ‘likely to have caused’ worst wildfires in Texas history
“One fire began when winds toppled a dead pine tree onto power lines, showering the dry vegetation below with sparks. The other fire ignited when fallen tree branches became tangled with power lines, showering dry grass and branches with sparks.”
- CBS: State Seeks $90 Million From PG&E For Wildfire
“California officials say they will seek more than $90 million in firefighting costs from Pacific Gas & Electric Co. after finding that a deadly 2015 fire was sparked by a tree that came into contact with a power line.”
What if you had a solution that you could easily install and implement to help you move away from planned scheduled maintenance to a condition-based maintenance program, a far more efficient maintenance strategy? A solution that could also help you allocate O&M dollars to the areas that need the most attention, while, more importantly, minimizing and mitigating risks and hazards for electrical line workers?
How Aclara Grid Monitoring Platform with Predictive® Grid Analytics software can help you improve reliability indices and track your WPCs
A monitoring solution with sensors like Aclara’s gives distribution operators monthly trends for categorizing performance event types. The platform also continually monitors and reports on the performance of circuits. Armed with this information, utilities, and network operators are able to implement cost-effective and rapid improvement plans, such as targeted tree trimming activities, early replacement of failing equipment and load balancing.
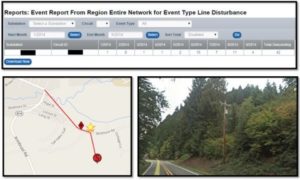
To learn how Aclara’s Grid Monitoring platform can help you:
- Proactively monitor circuits for more accurate patterns of faults and power outages
- Take steps to mitigate and prevent these issues before the circuit becomes a WPC