Certification is not as dark an art as many may suggest! Put simply, it’s all in the requirements.
As a manufacturer of products for Hazardous environments, product certification is a fundamental and crucial attribute to our products. We pride ourselves in manufacturing quality products which meet our end users’ needs. By meeting the requirements of certification, we ensure that the function and quality of our products is at the high level required to suit the demands of Harsh and Hazardous environments. This blog is aimed at shedding some light on the processes required to design for and achieve certification of Hubbell products.
Through the product design process, along with end user requirements and ease of installation, certification requirements are considered right from the very early stages. This ensures that our products are suitable for use in Harsh and Hazardous Environments and remain functionally compliant throughout the product lifetime.
The Certification Process
The process of certification requires attention to detail. During the design stage, all the relevant requirements are reviewed in detail by the engineering team. The inhouse review is a critical path in the certification process, this allows us to identify any potential challenges at the design stage prior to certification with third parties. If the review highlights any issues, the engineering team discusses solutions and ideologies for moving forward. Examples of challenges may include ensuring that the temperature range of the material selected is fit for purpose and alternative materials are considered and re-evaluated.
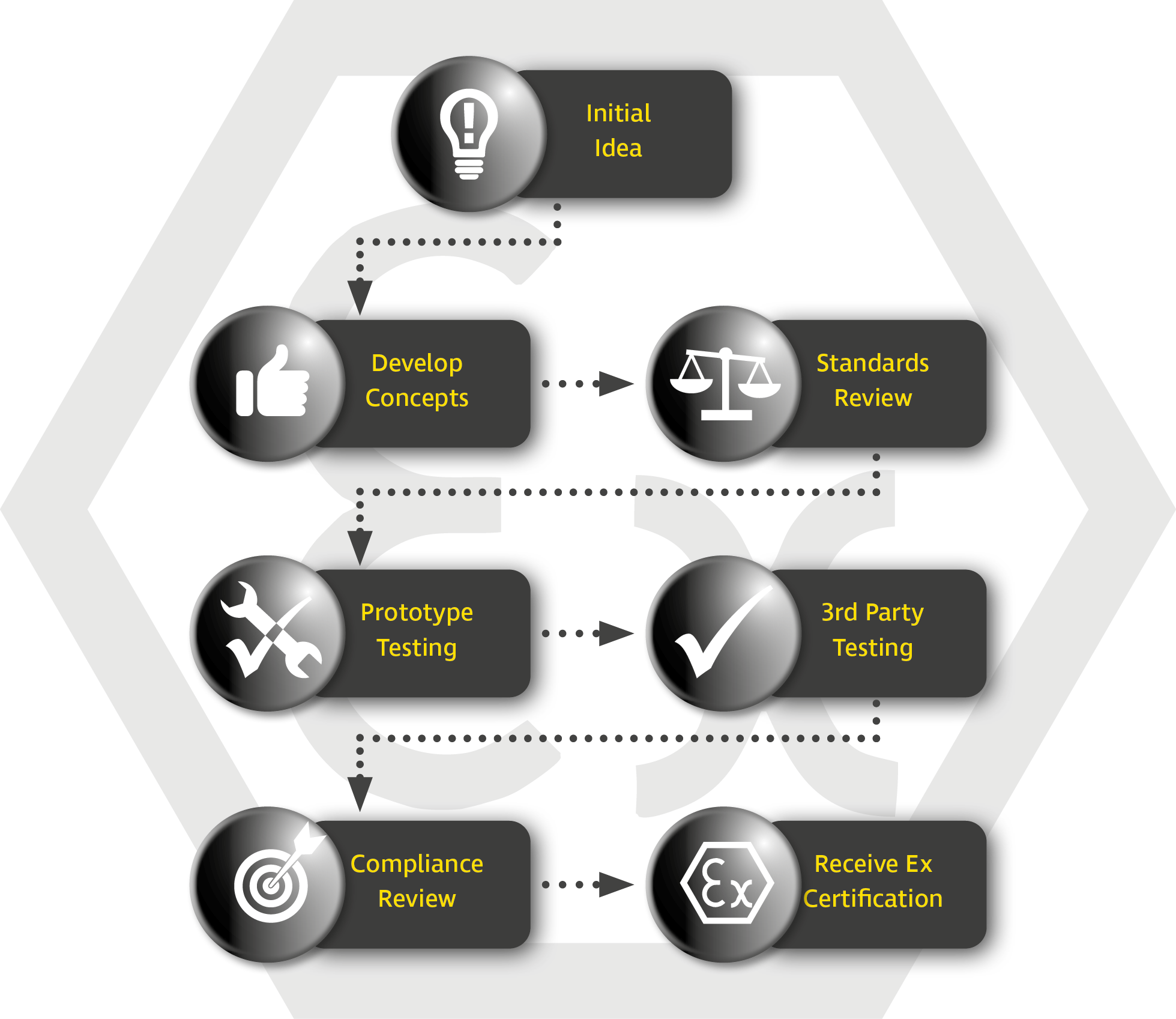
As part of the process, first ad hoc testing is performed to develop the product concepts to a point where it is demonstrated to meet both the testing and the end user requirements set by the brief. Once the design is set, the product is then tested by the third party test house who will be providing the certificate. By first developing the product using the correct testing processes, issues through the third party testing is minimised, resulting in a smooth testing process.
Once testing is complete, and a compliance review has been performed, the third party approval body will be in a position to release a certificate. This certificate allows us to mark the product suitable for use in areas where specific approvals are required. Hawke has a long history in achieving a wide range of approvals around the world (ATEX, IECEx, UKEx, EAC, Inmetro to name a few). This results in a globally approved product range which can be distributed throughout the world.
Minimising Certification Challenges with a Collaborative Approach
Communication is a key component of our approach to product approvals. By working closely with third party approval bodies, and maintaining an open approach, challenges throughout the approval process can be resolved swiftly and compliance of the products maintained. This is crucial in a world where the requirements of different countries vary, and the standards themselves are constantly under review. The recent challenge of Brexit and the UKCA mark is a great example where Hawke was in a position to react quickly to the new requirements, and work with third parties to quickly get necessary approvals in place.
Third-Party Certification Process
Third-party certification is independent of manufacturers and all requirements of the applicable protection concepts are applied during the assessment. To aid the third-party, we provide the relevant documents and drawings which form what is known as the "technical documents". These are assessed and if deemed suitable controlled via certification. The controlled documents are termed schedule drawings, and these cannot be altered without the involvement of the third-party. Apart from documentation, samples of specific designs are also provided so that they are subjected to type tests. These type tests are specific to the applicable protection concept. Type tests may include but are not limited to explosion tests, pressure determination tests and or material endurance tests; all of these form part of the certification process.
Understanding Market Requirements
It is also our duty to ensure that we are aware of the different requirements in specific markets. These requirements are discussed and considered depending on the target market. Since some regional approvals often require specific requirements, be it from a design aspect to marking requirements; in all cases these specific requirements are considered as part of the inhouse review. In addition to the inhouse discussions, we are also involved in standard committees, and this allows us to stay informed of any technical changes which are likely to impact our products. As with everything, preparation and participation are key.
Once all the relevant type testing is successfully performed, and the evaluation of product requirements completed, a product certificate is released by the third party test house. The applicable documents are then published to the website so they are readily available to our customers.
Keeping Up With Evolving Certification Requirements
The certification process does not end there - we are continually reviewing the relevant requirements to make sure that any changes made within the standards do not affect our products. If there are changes which are applicable then all the necessary steps to ensure compliance is maintained are taken.This pro-active approach in maintaining to latest standards ensures it is straightforward for our end users to also maintain their own installations to the most current requirements.
By striving to offer compliance across a range of different markets and global locations, we believe we offer our customers a market leading product range in terms of application and approvals. On a daily basis, challenges pertaining to certification are discussed with the aim of providing solutions which enhance products with relation to customer base. Ultimately, safety is the key attribute for products manufactured for use in hazardous areas. By ensuring we are thorough in evaluating certification requirements, and robust in the development and testing processes, we can make sure Hawke products continue to be market leaders in hazardous area applications.